Meyer impresses
Trouser manufacturer Meyer recently invited Texcon members to its factory in Romania. We chatted with three of them.
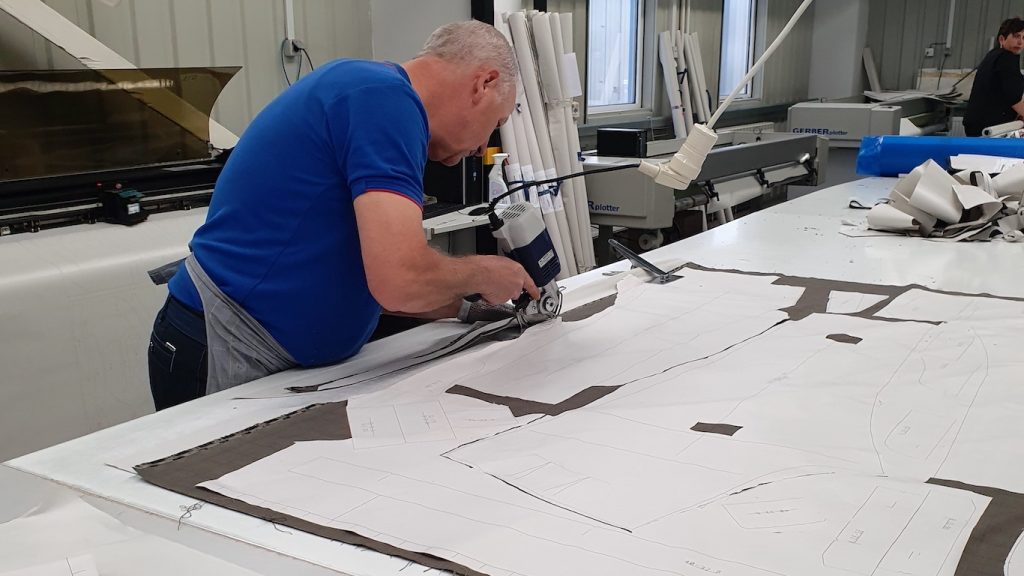
Since opening for business in 1960, Meyer has set itself apart as one of Europe’s leading specialists in men’s trousers. All its trousers are made in a small town in the Romanian countryside just a short drive from Brașov.
The factory, along with its 1,800 strong team, is impressive – something many Texcon members found out when they visited back in May:
“This factory maintains high standards and demonstrates a strong social commitment to its employees. They have a nursery and also offer their employees healthcare,” explains Lars Sønstebø, who runs Kase Moss and the gentleman’s outfitter “Herreavdelingen” at the Manglerud Senter mall in Oslo.
“Even the belt loops were ironed so that they were nice and smooth, they weren’t just sewn straight onto the trousers”
Lars Sønstebø
“We can see with our own eyes how things are: everything is well organised and the working conditions are good. I would have no problem saying to a customer that this is a place with good and safe conditions,” states Stig Rolfsen, owner and manager of Rolfsen.
Elin K. Tvete, the proprietor of Sarpsborg retailer Tvete, agrees, adding:
“We’ve been selling Meyer trousers for years, so it was fantastic to see how they’re made. The factory is enormous, bright and spacious, and there were so many people! They took real pride in the product they were creating.”
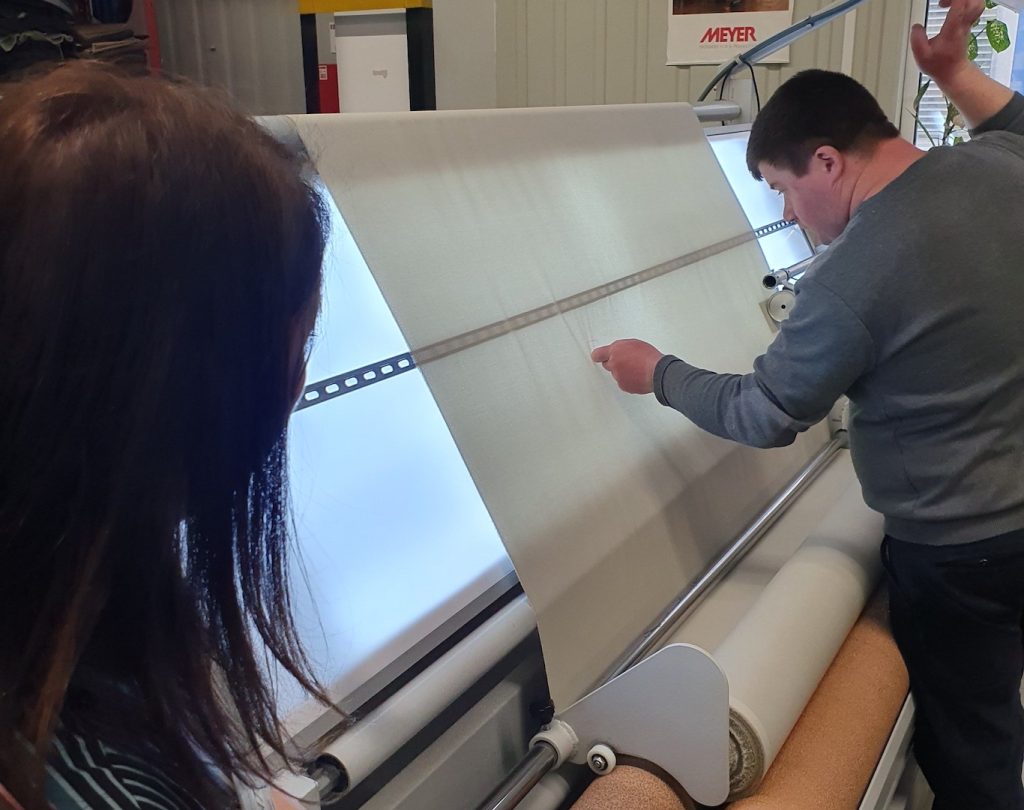
Making chinos
By closely following the production process, the visitors got to see first-hand how Meyer trousers are made.
The tour started on the top floor of the factory where the trousers are designed, and then followed the entire flow through to the finished product. The trousers go through all sorts of processes: sewing machines, washing, pressing and steaming – there was even someone brushing the trousers by hand once they were finished.
“We went through the around one hundred steps it takes to produce a regular pair of chinos. Even the belt loops were ironed so that they were nice and smooth, they weren’t just sewn straight onto the trousers,” says Sønsterud.
One highlight for Rolfsen was seeing two people performing quality control on the fabrics to see if there were any mistakes in the weaving:
“I reckon I could’ve looked at those rolls all day without noticing any mistakes, but they found them. It really impressed me, and really left me wondering what these guys must spot when they lie in bed at night staring at their ceilings…”
“We can see with our own eyes how things are: everything is well organised and the working conditions are good. I would have no problem saying to a customer that this is a place with good and safe conditions,” states Stig Rolfsen, owner and manager of Rolfsen.
Elin K. Tvete, the proprietor of Sarpsborg retailer Tvete, agrees, adding: “We’ve been selling Meyer trousers for years, so it was fantastic to see how they’re made. The factory is enormous, bright and spacious, and there were so many people! They took real pride in the product they were creating.”
What we do when washing our clothes
Meyer has a real commitment to the sustainability of the piece goods that are used and prioritises low water consumption in its production processes. All trousers are washed in large washing machines that can take around 120 trousers at a time, and the water goes through a filtering process before it is used again.
“Meyer is already 100% climate-neutral and doesn’t purchase wool from producers that are not able to guarantee proper animal welfare,”
Elin K Tvete
“After the wash had ended, there was a woman there brushing the lint off the pockets. Everyone had a task, and they were extremely efficient,” notes Tvete.
“And it’s manual work. You’ll see someone there with an iron and this ironing board that blows air from below. It all happens pretty quickly,” says Sønsterud.
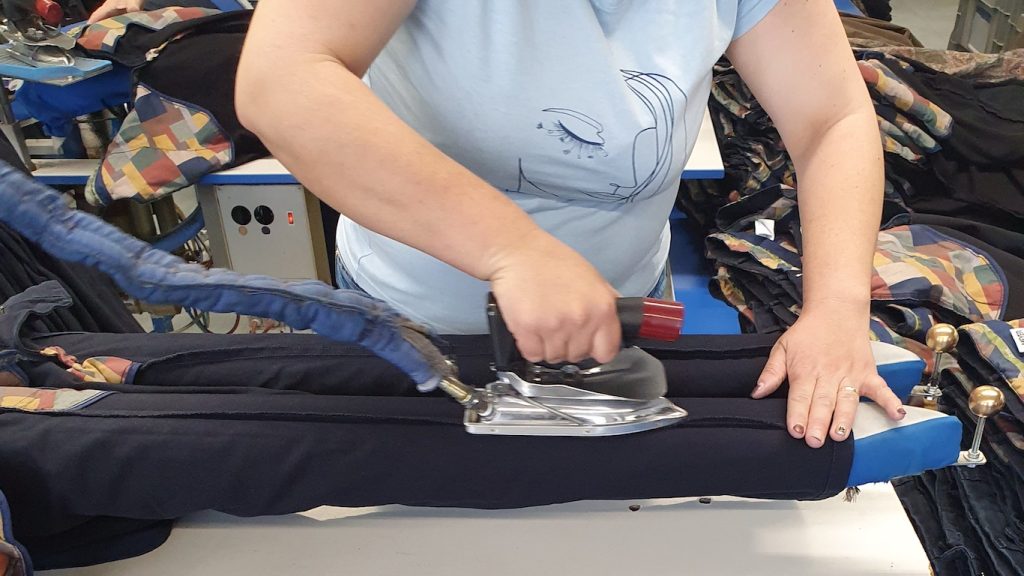
“If a customer ever says: ‘God, these trousers are a just too expensive,’ I can look them straight in the eye and tell them what they’re getting for their money. It’s bordering on pure craftsmanship,” says Rolfsen
Ground-breaking cotton
Each pair of trousers has its own story before reaching the factory floor. When it comes to fabrics, Meyer have distinguished themselves by exclusively using 100% organic cotton in all of their collections.
The cotton is made using 40% less water, and this is beneficial for the environment and consumers as the cotton is grown without the use of harmful chemicals, fertilisers or genetically modified seeds.
Rolfsen points out that Meyer was chosen as one of the most forward-thinking textile manufacturers in Europe when it comes to the environment:
“It’s impressive to see that they are in the vanguard in their industry, instead of always playing catch-up with new rules and regulations.” “Meyer is already 100% climate-neutral, and they don’t purchase wool from producers that are not able to guarantee proper animal welfare,” explains Tvete.
Unique belt details
Meyer also has an exceptional eye for detail, which helps create the quality that they are known for. They have always used seven belt loops where others use five, which lets the belt sit better and more comfortably around the waist.
“Even the inner waistband on Meyer trousers is made up of many layers so that your shirt doesn’t slide up, as it sits at the waistband, which holds in place,” explains Sønsterud.
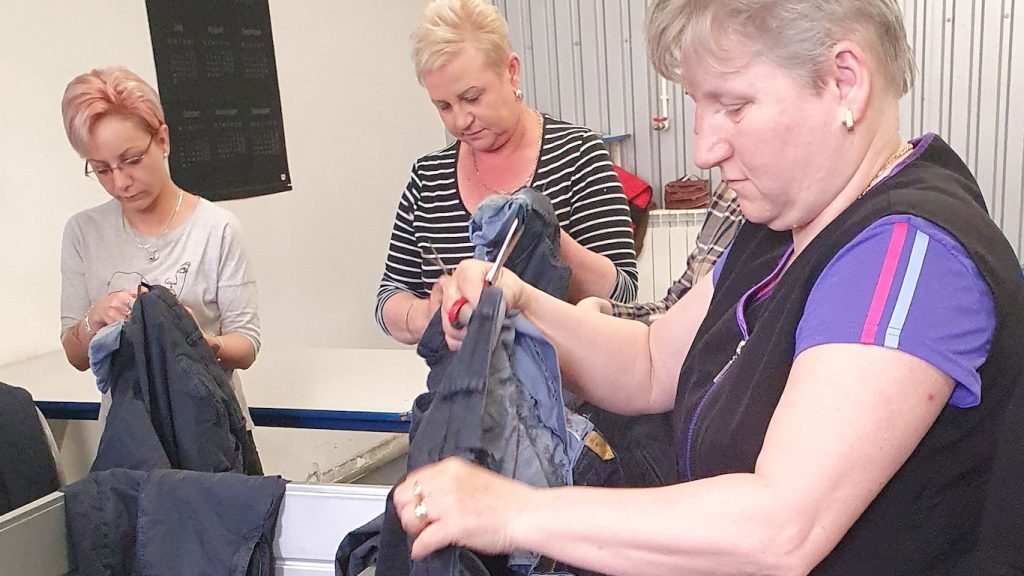
Meyer’s M|5 series, which are cut a little slimmer than Meyer trousers, are designed to entice younger customers:
“We had this young person come in and buy four pairs of Meyer trousers,” says Rolfsen.
“The trousers for Norway are hanging just down there”
The members of the tour party bring up a particularly fun experience, where they got to take a look at the warehouse filled with finished trousers.
“It’s bordering on pure craftsmanship; their professionalism is imbued in every single thread”
Stig Rolfsen
“There were racks for Norway, Sweden and Finland in sections and Stig, Elin and I were in the ‘Norwegian row’,” says Sønsterud.
“They said: “The trousers for Norway are hanging just down there” We found our own autumn shipment, with our name on it and everything. It was great!” Tvete chuckled.
Come along next time!
If there similar tours in the future, other Texcon members are encouraged to come along:
“It’s so interesting to see how things are made. These are products we have in our store, but you feel more ownership over them after you’ve seen how they’re made. We have always known that Meyer means high-quality, but now we can see why, and it’s because quality permeates every, single step of the process,” Tvete points out.
“Those of us travelling together also got a lot of input from each other, so the visit was really insightful and useful in a number of ways,” Sønsterud adds.